pdf Irradiation de trois agents dans une installation de traitement par ionisation (143 ko)
Circonstances
L'appareil en cause est un accélérateur électrostatique d'électrons, modèle Samson (2,5 MV, 35mA). Il était utilisé pour le traitement par ionisation de matériaux fluorés. Les débits de dose en fonctionnement nominal sont de 80000 Gy/s (électrons).
L'appareil a été acheté d'occasion aux USA, par une société X qui l'a implanté en France, puis revendu à nouveau à une entreprise Y de stérilisation par irradiation. Le marché n'est pas porteur, la société est revendue à un particulier Z. Après redressement puis liquidation judiciaire, un tiers, PDG d'une société locale, rachète les murs et l'appareil et crée une nouvelle société T dont l'objectif est le traitement de matières fluorées sous irradiation. Cette société changera par la suite de dénomination T.
Dans ce parcours complexe, on retrouve une personne, conseil de la première entreprise de stérilisation, qui devient le DG de la nouvelle société.
Il n'y a pas de preuve que cet historique joue un rôle dans la survenue de l'accident.
Cependant, il convient de noter qu'il existe un certain nombre d'anomalies :
- La cuve métallique sous pression (8 bars) de l'accélérateur n'apporte pas la preuve qu'elle a subi les essais réglementaires sous pression : absence de poinçons.
Plusieurs malfaçons et non-conformités électriques ont été constatées par un organisme de contrôle, diligenté à l'initiative des repreneurs (Z ou T).
La DRIRE locale est avisée, signale ces infractions au Procureur de la République, demande les sanctions.
La société T échappera aux contraintes réglementaires en diminuant la HT de fonctionnement (2,3 MV → 1,7 MV) et la pression (8,3 bars → 4 bars). - Le bâtiment n'est pas prévu pour recevoir cet appareil. Cela va entraîner des contraintes au niveau de la trajectoire du convoyeur.
- Le convoyeur est un convoyeur classique, non prévu pour travailler sous rayonnements : les huiles de graissage, les matières plastiques le composant se dégradent sous l'effet des rayonnements, certains matériaux s'oxydent au contact de l'ozone produit par ionisation de l'oxygène.
Mode de fonctionnement : sécurités
Lorsque l'appareil doit être mis en marche, l'opérateur effectue un parcours obligé qui le conduit à activer un rondier témoignant de son passage, à fermer des portes munies de « fins de course » ou d'un système optique, avant de pouvoir passer la clé de commande du pupitre de la position «arrêt» à la position «marche». Le parcours doit être effectué en moins de trois minutes sous peine d'être repris à sa phase initiale. L'accélérateur est ensuite placé en position « haut voltage ». Puis le faisceau est délivré en tournant la clé sur « Beam Current ». L'arrêt complet de l'appareil conduit à un arrêt programmé de l'installation de 15 minutes (temps nécessaire pour l'évacuation de l'ozone produit par l'ionisation de l'air).
Pour éviter cette procédure pénalisante, avant d'intervenir pour réparer une gaine de ventilation située à l'aplomb du scanner (dispositif de balayage du faisceau d'électrons), sous celui-ci, la décision a été prise de laisser la clé de commande en position « high voltage ». Dans cette position, l'alimentation du filament de tungstène (sources d'électrons) est coupée, mais la haute tension accélératrice est maintenue. Le courant qui traverse alors l'accélérateur est très faible (courant résiduel) mais des débits de dose voisins de 0,1 Gy/s subsistent. Par ailleurs, pour pénétrer dans le local sans passer par la porte métallique (ce qui arrêterait l'installation), les intervenants ont l'habitude de passer par la sortie du convoyeur qui ne dispose pas de détecteur d'intrusion.
1er accident
Un bac en aluminium, contenant des produits fluorés, se bloque sous le scanner. Les produits s'enflamment, la fenêtre en titane du scanner est endommagée (elle sera remplacée).
Le chef d'équipe C, muni d'un masque pour se protéger de l'acide fluorhydrique (créé par interaction de la vapeur d'eau et du fluor dégagé par les produits), pénètre dans la salle d'irradiation pour éteindre l'incendie.
L'origine du blocage provient de la conception générale du système de convoyeur, de la petite taille relative des bacs par rapport à la largeur du convoyeur (les bacs ont tendance à se mettre en travers), de la déformation des bacs sous l'effet de la chaleur (faible épaisseur d'aluminium).
2e accident
La gaine de ventilation en cause, en aluminium, est fragilisée par les rayonnements subis. Elle est cassante et friable. Elle a déjà été réparée avec du ruban adhésif.
L'intervention en elle même s'est déroulée de la manière suivante :
M. A pénètre par la sortie du convoyeur pour réparer la gaine de ventilation. Au bout d'un quart d'heure d'essais infructueux, le chef d'équipe envoie M. B puis, finalement, intervient à son tour. Les trois intervenants passent à plusieurs reprises les mains, les avant-bras, la tête et le dos sous le scanner. M. A qui se tenait accroupi a eu également une exposition des jambes.
Conséquences radiologiques
Les films dosimètres réglementaires n'ont fait l'objet d'un développement qu'après l'apparition, chez les trois accidentés des premiers symptômes d'irradiation aiguë. Les équivalents de dose mesurés se situent aux limites du noircissement total des films dosimètres. Aussi, les valeurs fournies ne sont que des approximations. En outre, ces valeurs ne représentent pas les doses maximales subies dans la mesure où les dosimètres (portées à la poitrine) n'étaient plus soumis au faisceau primaire des électrons notamment lorsque les intervenants passaient la tête et le dos sous scanner.
Nom | Peau | Organisme entier |
---|---|---|
M.A | 40 Sv | 1 Sv |
M.B | 9 Sv | 250 mSv |
Chef d'équipe | 5 Sv | ? |
Le chef d'équipe remarque deux jours après une coloration anormale de ses deux mains et de son front. Peu de temps après, il perd ses cheveux progressivement sur le haut du crâne. Deux semaines après, il constate la présence d'un phlyctène de la main droite (soulèvement de la peau sous laquelle se trouve un liquide translucide). L'atteinte gagne ensuite les deux mains et avant-bras puis le thorax et le front. Les brûlures radiologiques couvraient 14 % de la surface cutanée, mais elles n'ont pas nécessité d'autogreffe.
M. B a ressenti des démangeaisons au cuir chevelu dès la fin de son intervention (1/4 h). Rapidement il est anormalement bronzé et perd ses cheveux. 2 semaines plus tard, les cloques descendaient dans le dos et le long du tronc. Les brûlures radiologiques concernaient 25 % de la surface du corps. Des greffes de peau lui ont été faites.
M. A fut le plus gravement touché. La surface corporelle a été brûlée à 60 %. Ces brûlures touchaient la tête, le tronc, les épaules, toute la jambe gauche, la cuisse droite et les deux bras. Pendant 6 mois, dont 6 semaines de coma, il a été placé en chambre stérile. Il a reçu une quinzaine de greffes.
Analyse de l'arbre des causes
L'arbre des causes, dans une hypothèse de construction vraisemblable, montre deux grandes chaînes causales : une chaîne liée à la conception du matériel, une chaîne liée au comportement des opérateurs.
Matériel et installation
Le convoyeur, la ventilation, n'ont pas été conçus pour fonctionner sous rayonnements. D'où des pannes régulières nécessitant des interventions.
La chaîne de sécurité présente une faille, puisqu'on peut entrer dans le local par la chicane de sortie du matériel.
Cette introduction n'est d'ailleurs pas sans risques, du point de vue classique, puisqu'il faut escalader 3 fois le convoyeur pour arriver jusqu'au scanner.
L'appareil n'avait pas été déclaré à l'Inspection du Travail.
Comportement des opérateurs et de la direction de l'entreprise
Selon les témoignages recueillis au cours du procès qui a suivi l'accident, les trois opérateurs avaient l'habitude d'entrer dans la casemate par le sas de sortie du matériel, suivant en cela l'exemple du directeur général. Les raisons en sont la perte de temps occasionnée par la procédure officielle (recherche de productivité ?), et la méconnaissance profonde des risques, ou l'accoutumance.
Le personnel n'a reçu aucune formation aux risques, sauf peut-être chimiques (crainte du HF).
Leçons à tirer de l'incident
Il est évident que la réglementation en vigueur n'était pas respectée :
- Le générateur électrique de rayonnements ionisants n'était pas déclaré à la DRIRE. Mais il était connu de la DRIRE, qui avait demandé au procureur de la République des sanctions. Ceci n'a rien changé en terme de risque potentiel (les doses subies auraient été encore plus élevées si l'appareil avait fonctionné en régime nominal). Le contrôle initial obligatoire avant mise en service, par un organisme agréé, n'avait pas été réalisé.
- L'absence de désignation par l'employeur d'une personne compétente, laquelle doit avoir préalablement suivi avec succès une formation à la radioprotection et à qui il revient de procéder à l'analyse périodique des postes de travail, de veiller au respect des mesures de protection, de recenser les situations susceptibles de conduire à des expositions exceptionnelles ou accidentelles, de participer à la formation à la sécurité des travailleurs exposés. Mais aurait-elle eu les moyens d'améliorer la sécurité du système ?
- L'absence de formation et d'information des intervenants par l'employeur. On rappelle que celui-ci est tenu d'organiser la formation à la radioprotection des travailleurs exposés et de leur remettre une notice écrite même s'ils sont appelés à pénétrer occasionnellement dans la zone contrôlée.
- Les signalisations appropriées destinées à informer les travailleurs sur les risques encourus étaient rédigées en langue anglaise.
- Les personnels étaient intérimaires. La réglementation propre aux travailleurs à statut précaire n'était pas appliquée.
- Ils étaient classés catégorie B, sans fiche d'aptitude, sans visite médicale préalable.
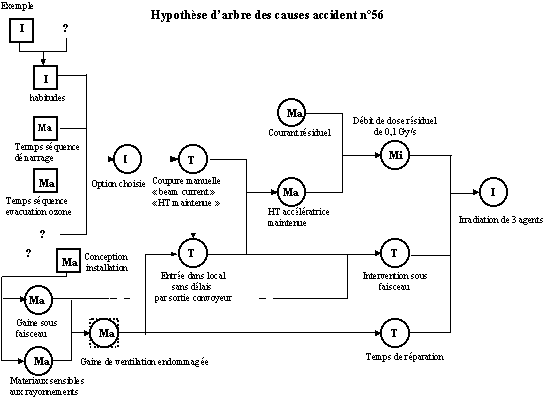
pdf Irradiation de trois agents dans une installation de traitement par ionisation (143 ko)